In the realm of inspection, be it for rolling stock, facilities, or infrastructure, the lack of organized photo archiving frequently results in wasted time and the loss of critical information. To address this challenge, the adoption of an inspection app is paramount. By standardizing and automating photo-taking processes, such tools streamline operations and facilitate seamless access to critical data, enhancing efficiency and informed decision-making.
STREAMLINING INSPECTION: PHOTO ARCHIVING AUTOMATION
At SYSTRA Canada, we are committed to going digital and paperless, enhancing efficiency and sustainability through automated workflows. Leveraging cloud-based solutions like SharePoint for centralized data management, we streamline processes from data entry to report generation. Our own development, PowerApps, integrates seamlessly with Microsoft, offering support and modularity for tailored solutions. This approach not only boosts operational efficiency but also underscores our dedication to innovation and environmental preservation.
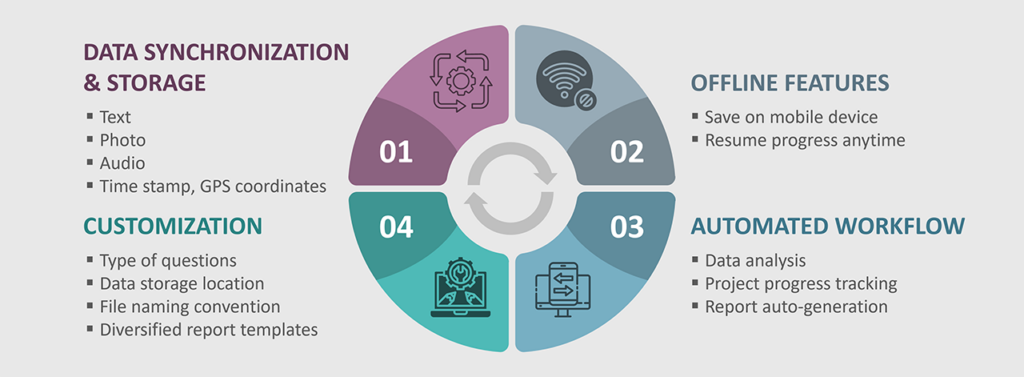
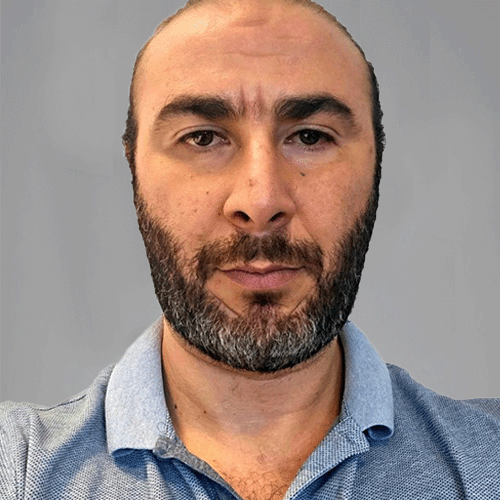
This tool enables seamless association of photos with inspection tasks, facilitating efficient filing in SharePoint. It optimizes time management upon returning to the hotel and facilitates real-time sharing of inspection results internally or with clients.
Mohamed El Otmani, Rolling Stock Lead, Locomotive & Wagon
The capability to meticulously archive pictures in real-time on SharePoint significantly enhances efficiency during inspection visits.
Adrian FAUR, Team Lead, Electrical Engineering
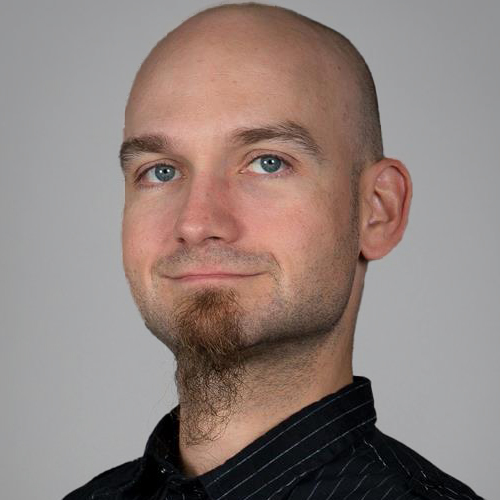
INSPECTION INNOVATION: DIGITAL CHECKLISTS FOR STREAMLINED EFFICIENCY AND COLLABORATION
This application is well-suited for inspection scenarios, enabling the digitalization of checklists and empowering users to utilize their own or company-provided mobile devices (such as tablets or smartphones) for task execution.
In addition to capturing text and numerical data, users can seamlessly capture and store photos and voice recordings, automatically organized into designated folders in SharePoint. Should interruptions occur during inspections, users can conveniently save checklists as drafts for later completion.
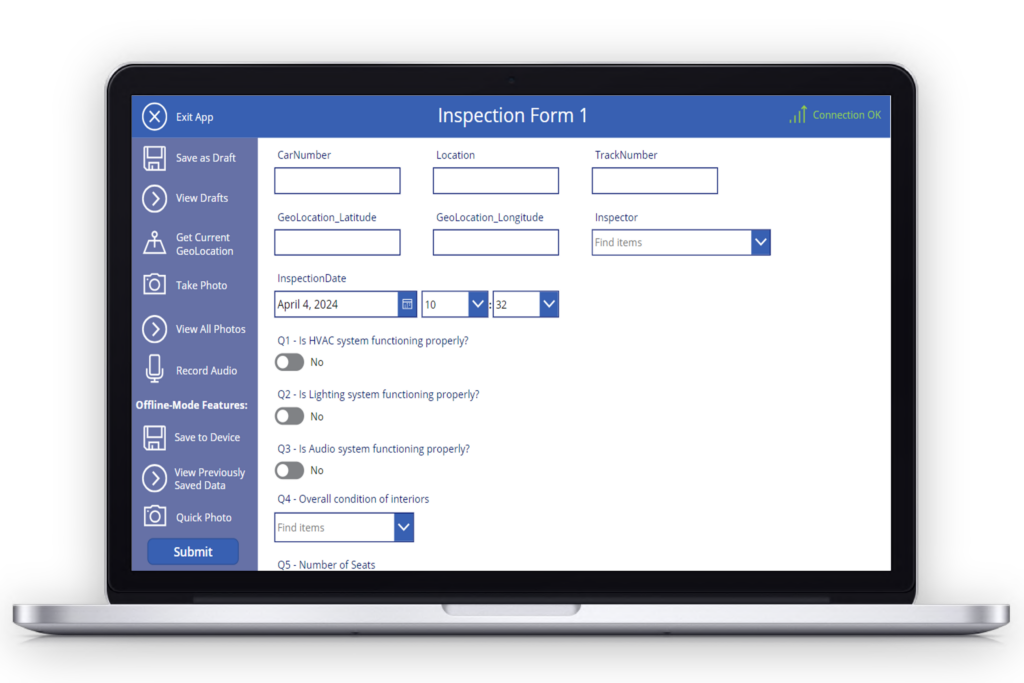
The app’s offline mode ensures continued functionality in areas with poor or no internet connectivity, allowing intentional offline work to conserve cellular data. Furthermore, its intuitive interface supports collaborative efforts, facilitating simultaneous work by multiple individuals. An added advantage is the potential for workflow automation, enabling report auto-generation through Power Automate Workflows. While the app can be customized for various scenarios (e.g., different rolling stock cars, bridges, tunnels, catenary systems), it’s important to note that the PowerApps platform may not be suitable for inspections requiring extensive video recordings due to file size limitations for SharePoint uploading.
PAIN POINTS AND SOLUTIONS
PAIN POINT
The conventional inspection method, reliant on pen and paper alongside cameras for photo documentation, encounters significant hurdles in industrial settings where conditions like grease and dust often obscure vital information. Moreover, the burden of carrying multiple papers and tools becomes cumbersome, particularly in situations requiring extensive mobility.
SOLUTION
Embracing a paperless approach, inspectors can streamline tasks using a single mobile device, such as a tablet, enabling seamless performance at any location and time.
PAIN POINT
Post-processing of documents can prove time-consuming, involving manual data entry, analysis, parsing, and report completion, especially in cases of repetitive inspections. Manual operations, often carried out by different individuals, introduce inconsistencies in photo naming and captioning, leading to disorderly archiving and difficulties in retrieving information.
SOLUTION
By maximizing automation, we minimize the need for manual intervention in repetitive tasks, significantly reducing the occurrence of human errors.
PAIN POINT
The risk of data loss during the interval between inspection conclusion and post-processing commencement, prompted by travel or unforeseen circumstances, is a valid concern.
SOLUTION
Our approach ensures instant accessibility for team members, while providing enhanced control and traceability over data modifications, mitigating the risk of loss and ensuring data integrity throughout the inspection lifecycle.
BENEFITS FOR USERS
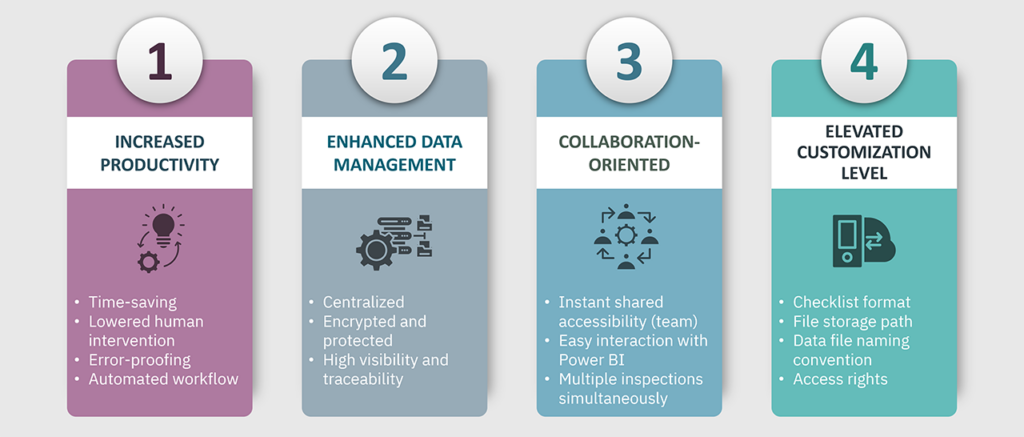
LOOKING AHEAD
The tool originally developed for internal processes has the potential to be optimized and repurposed for marketing purposes. Furthermore, forthcoming enhancements will include support for video recordings exceeding 50MB, sophisticated photo annotation functionalities enabling the addition of detailed notes and markups directly onto images, and the implementation of a comprehensive review and approval process.
This transformation promises to yield reductions in bid costs and operational expenses while enabling the seamless delivery of reports in real time.